Service for cages
We currently have four certified service stations for aquaculture in Norway. The service stations are located in Svolvær, Måløy, Solund and Uskedal, are zero-emission stations and approved under NS 9415, the NYTEK regulations and our internal competence programme, which contributes to ensuring the quality of our services.
At the service stations, we offer environmentally friendly service for fish farming cages in the form of cleaning, mending, impregnation, drying and covered storage. In the washing process, we use new cleaning systems that separate out special waste and clean the water being used. The waste is sent for approved special waste processing, and our customers can thus feel secure in knowing that service on their cages does not give rise to emissions from our service stations.
The service station lies right at the edge of the quay at Trollebø by Måløy furthest out in Nordfjord.
- AquaStructure-certified service station
- Substantial activity involving service of fish farming cages and lice skirts
- Zero emissions station
- Impregnation with vacuum impregnator
- All employees have been trained with respect to Selstad’s quality assurance programme and are checked annually in both internal and external audits
The station lies right at the edge of the quay at Ytrøygrend in Solund.
- AquaStructure-certified service station
- Substantial activity involving service of fish farming cages and lice skirts
- Zero emissions station
- Impregnation
- All employees have been trained with respect to Selstad’s quality assurance programme and are checked annually in both internal and external audits
The service station is located at Uskedalen in the Municipality of Kvinnherad.
- AquaStructure-certified service station
- Substantial activity involving service of fish farming cages and lice skirts
- Zero emissions station
- Impregnation with vacuum impregnator
- All employees have been trained with respect to Selstad’s quality assurance programme and are checked annually in both internal and external audits
The station lies right at the edge of the quay at Svinøya at the centre of Svolvær.
- AquaStructure-certified service station
- Substantial activity involving service of fish farming cages and lice skirts
- Zero emissions station
- Impregnation with vacuum impregnator
- All employees have been trained with respect to Selstad’s quality assurance programme and are checked annually in both internal and external audits
Our service stations
- All our service stations are located directly at the wharf’s edge and are easily accessible by both land and sea.
- All employees have been trained with respect to Selstad’s competence programme and are checked annually in both internal and external audits.
- The service stations are AquaStructures-certified for performing service.
- Our service stations are zero-emission stations.
- We perform service on fish farming cages and lice skirts.
- All the service stations impregnate with vacuum impregnation.
We place an emphasis on developing our business through close co-operation with our customers and suppliers, and annual audits and certifications of the service stations, including NS-EN ISO 9001:2015, NS EN 9415, NS-EN ISO/IEC 17020 and NS-EN ISO 14001:2015.
Environmentally friendly service with no emissions of wastes
At the service stations, we offer environmentally friendly service for fish farming cages in the form of cleaning, mending, antifouling, drying and covered storage. In the washing process, we use new cleaning systems that separate out special waste and clean the water being used. The waste is sent for approved special waste processing, and our customers can thus feel secure in knowing that service on their cages does not give rise to emissions from our service stations.
Competence programme for quality assurance of service
We have designed an internal competence programme for the production employees at our service stations. This programme ensures the proper competence and hence thus the quality of the service we provide, and we have now been running it smoothly for five years at all our service stations. The competence programme accords with the requirements in NS 9415 and the NYTEK regulations, and includes training, repair certification, professional certification and annual follow-ups. This provides new employees with the training and follow-ups they need, thereby ensuring a high level of professional competence on an individual basis.
Impregnation
We offer impregnation and coating from familiar suppliers such as Steen-Hansen, NetKem and Brynsløkken. Vacuum impregnators are used at our service facilities, providing optimum uptake of impregnation and shorter drying times. The procedures and consumption factors we utilise are in accordance with the recommendations of the manufacturers, ensuring the optimum antifouling effect on the fish farming cages.
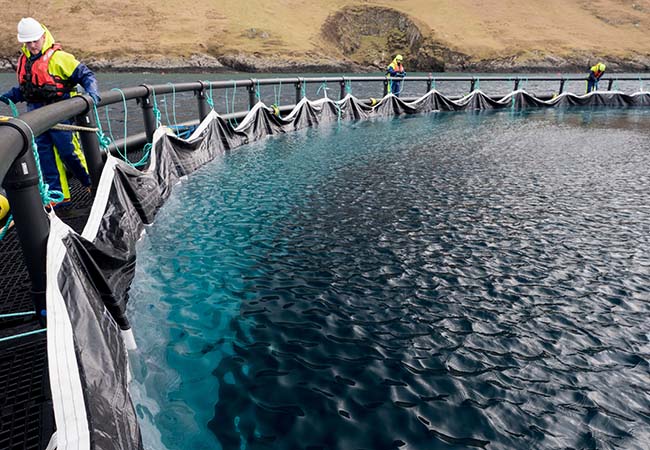
Lice skirts that tolerate service
Our service stations are certified for performing service on lice skirts, and place a special emphasis on the environment and quality in their service processes. We deliver specially designed lice skirts in accordance with your needs and desires, and work continuously to develop our solutions still further. Our lice skirts are designed with a special emphasis on a long lifespan in unsheltered locations, and for the quality of the skirt to also be able to be maintained during the service process.
We perform service for lice skirts at all our service stations for aquaculture; in Svolvær, Solund, Måløy and Uskedal. Our service stations have zero emissions so our customers can be confident that service on their lice skirts will not have negative environmental consequences. Environmentally friendly cleaning processes ensure zero emissions of polluted process water and other waste, and for the entire time we are following our Environmental Standard: NS-EN ISO 14001:2015.
The service process consists of receiving products before they are forwarded for washing and disinfection. Here, we make use of Decanter technology where the wash water is assessed during the process such that the skirt is not washed more than necessary. Subsequently in the process, the lice skirt is dried before it is shipped to a new department where the skirt is repaired and lead, chains and other hardware are replaced.